Chemiluminescent immunoassay (CLIA) kits have become indispensable tools in modern clinical laboratories, thanks to their high sensitivity, specificity, and automation potential. Whether you're screening for infectious diseases or monitoring tumor markers, understanding how these kits work and how to choose the right one is critical for reliable results and efficient diagnostics.
1. Overview of Chemiluminescent Immunoassay Kits
Chemiluminescent immunoassay kits detect specific antigens or antibodies based on a luminescent chemical reaction. Here’s how it works: an antigen-antibody binding event is coupled with a chemiluminescent substrate that emits light when catalyzed by an enzyme. The emitted light is then measured using a luminometer, with the intensity proportional to the concentration of the target analyte.
Application Areas:
- **Clinical Diagnostics**: thyroid function tests, cardiac markers.
- **Infectious Disease Testing**: CRP, SAA, IL-6, PCT, KL-6, HBP, COVID-19 antibody/antigen detection.
- **Tumor Marker Detection**: PSA, AFP, CA125, and more.
- **Cardiac**: D-dimer, BNP, NT-proBNP, CK-MB, Myo, hs-cTnT, RF detection.
- *Fertility Tests*: beta-hCG, Prolactin, Prog, Cortisol, FSH, AMH, Testosterone, LH, Estradiol
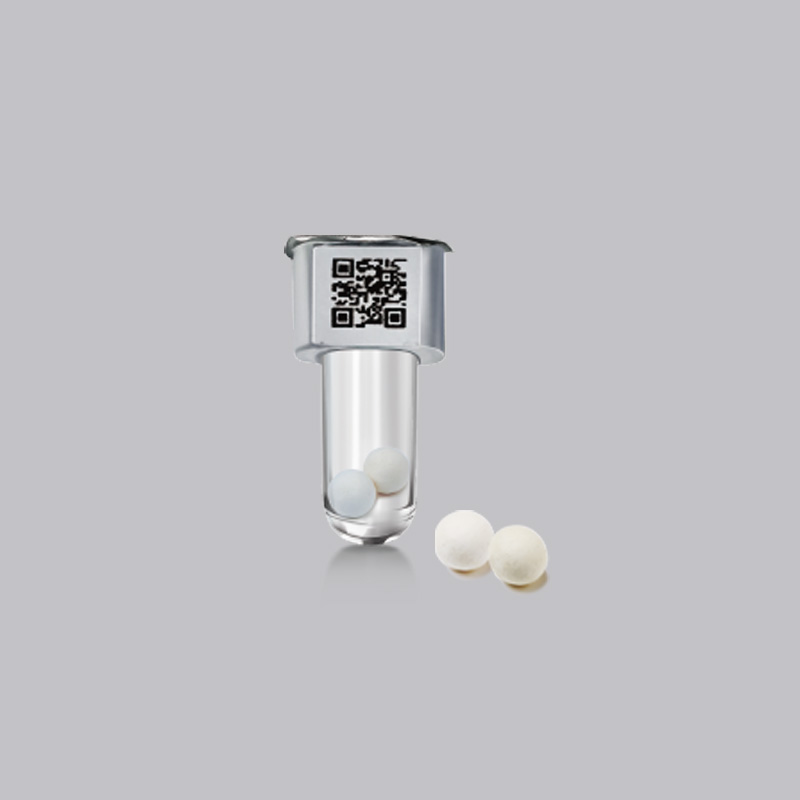
2. Selection Criteria and Considerations
### Sensitivity and Specificity:
The reliability of diagnostic results hinges on sensitivity (true positive rate) and specificity (true negative rate). High sensitivity ensures even trace amounts of biomarkers are detected, while high specificity reduces false positives. Always check:
- Sensitivity % (ideally >95%)
- Specificity % (ideally >95%)
### Detection Range:
Different kits are tailored for specific analytes. Make sure to align your selection with your lab’s testing focus:
- **Hormones**: TSH, LH, hCG
- **Viral Markers**: HBsAg, HCV Ab
Verify that the kit covers the necessary linear detection range for your sample type and concentration needs.
3. Product Quality and Certification
Quality assurance is non-negotiable in clinical diagnostics. Look for kits that carry:
- CE Mark (Europe)
- FDA Approval or EUA (U.S.)
- ISO 13485 certification for manufacturing processes
Additionally, consider the manufacturer's:
- **Reputation**: Years in the market, reviews, known partnerships
- **Production Standards**: GMP compliance, QC systems
- **Batch-to-batch consistency**: Crucial for longitudinal studies or repeated testing
4. Ease of Use
Modern CLIA kits are often designed with automation in mind, but workflow simplicity still varies. Evaluate:
- **Number of steps**: Manual vs. automated workflow
- **Sample preparation**: Plasma, serum, whole blood compatibility
- **Training Requirements**: Is the kit suitable for labs with limited technical personnel?
A good kit should offer intuitive instructions and come with technical support when needed.
5. Cost and Value for Money
CLIA kits vary in price depending on:
- Target analyte
- Brand reputation
- Certification level
While budget is important, avoid choosing solely based on price. Instead, assess:
- Cost per test
- Shelf life and storage conditions
- Bundled services or equipment availability
One of Poclight's strongest advantages is that our analyzer offer a simple one-step operation, making it highly user-friendly. Additionally, our kits eliminate the need for washing or separation processes, which not only saves time but also reduces the potential for errors. With minimal maintenance requirements, these kits are designed to facilitate smooth workflows, ensuring that even labs with limited technical personnel can operate them effectively.
Another strong advantage is the reagents is Lyophilized Beads NO COLD CHAIN NEEDED, NO refrigerators needed, with long shelf-life.
This guide provides a comprehensive overview to help you choose the right chemiluminescent immunoassay kits for your laboratory needs.